CEO Task Force's work to develop dust strategy for British Columbia's sawmills aims to ensure fatal explosion never happens again; actions include cleaning mills, gathering science on explosive dust conditions, developing control and audit mechanism
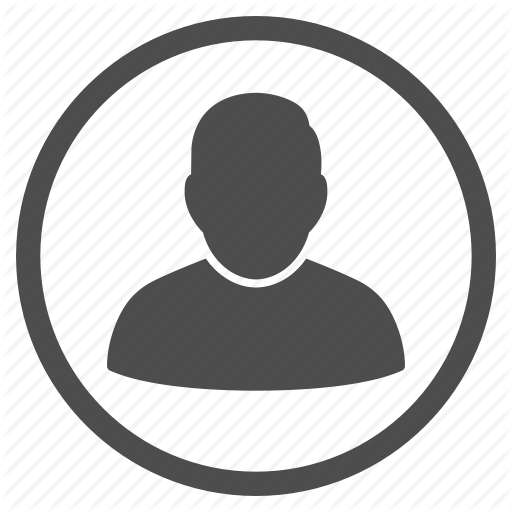
Wendy Lisney
PRINCE GEORGE, British Columbia
,
March 6, 2014
(Prince George Citizen)
–
On the morning of April 24, 2012, Canfor president Don Kayne awoke in Vancouver to a world that had changed overnight.
The violent explosion the night before at a competitor’s sawmill in Prince George, Lakeland Mills, was the second mill explosion within three months. Something - possibly sawdust from dry, beetle-killed timber - had turned two sawmills into deadly workplaces.
The Lakeland Mills explosion killed two and injured 22. It was by appearances nearly identical to an explosion three months earlier at Babine Forest Products at Burns Lake, that had killed two and injured 20. Although there was no proven cause, sawdust was the one element both mills blasts had in common.
As chief executive officer of one of the largest forest companies in North America, Kayne was one of the few people in British Columbia who had the power and the ability to do something about the risks to workers and mills posed by sawdust.
So when Hank Ketcham, chairman of rival West Fraser Timber, called later that morning about the explosion and its implications to the province’s forest industry, the two men decided that they needed to act.
They couldn’t wait, their employees couldn’t wait, for an inquiry to determine what had happened, said Kayne.
“There was understandably a lot of concern. That was huge, for the first while, to ensure employees felt confident that they were safe coming to work,” Kayne said of that first day.
If the two largest companies didn’t take the lead in showing that the industry was safe, who would?
“We have to put something in place to make sure that this never happens again,” Kayne recalled Ketcham saying in that first conversation. “We need to do something immediately, not in a week or two or three, we need something set up right away,”
Kayne and Ketcham called their fellow CEOs, chief executives from major lumber companies like Tolko, Interfor, Dunkley, Western Forest Products and Conifex. They set up a meeting at a nearby hotel.
By the end of the day, the CEOs had decided to put their rivalries aside and to take the unprecedented step of forming what became known as the CEO Task Force. Their mandate was to develop a strategy for dealing with dust in sawmills. If the sawdust issue were to be resolved, the new direction needed to be set from the top.
From that first meeting, the task force grew to include 12 of the province’s largest forest companies, representing 55 sawmills and 70 to 75 per cent of B.C.’s total lumber production.
The executives knew that they could not manage what they did not understand. It would take collaboration and a clear direction from them to track down the conditions that had turned sawmills into bombs. It would also require a coalition that included everyone. The task force wanted buy-in from workers as well as managers, which meant bringing in the Steelworkers Union.
Forest companies and the union were often at odds over workplace issues. This time, however, the union and the CEOs had a common objective: ensuring that sawmills were safe work places.
“Our workers needed assurances that whatever the hell happened there won’t happen again,” said Bob Matters, head of the Steelworkers Wood Council, recalling the days after the explosion. The Steelworkers have a national reputation for taking a tough stand on safety. The union fought a 12-year battle to amend the Criminal Code to include corporate negligence after the 1992 Westray coal mine explosion in Nova Scotia that killed 26 workers. Now corporations were asking the union to join them in finding a solution to explosions in B.C.
Matters was asked to join the CEO Task Force. The first thing to do was to clean the sawdust out of all the mills and then, with the immediate hazard removed, find out under what conditions sawdust becomes explosive, conduct a risk assessment at each mill and devise more effective ways of dealing with dust. Finally the task force wanted to establish a way of auditing dust mitigation measures to make sure the issue doesn’t return.
The task force used an already-established industry safety group, called MAG, the Manufacturers Advisory Group, to take on the combustible dust issue. Former Canfor chief forester Ken Higginbotham was brought out of retirement to head it in its new role.
The CEOs’ decision to own the issue meant that it was taken seriously at every level, Higginbotham said.
“The CEO group has been there as the steering committee to the whole thing,” he said.
Quite separately, WorkSafeBC was also requiring companies to undertake a risk assessment of all mills and to develop a wood dust control program. Further, the B.C. Safety Authority, responsible for the safe installation and operation of electrical and gas systems in sawmills, issued an order requiring mills to establish processes around dust build-up.
The directives from the regulators on sawdust management were the first indications to industry that wood dust was viewed as a key factor.
Canfor safety manager Ross Lennox explained how Canfor responded to both the MAG and the directive from the regulators.
“We brought together a team of people from across Canfor, it involved people from across all of our operations.
“We also involved technical experts and engineers who have been trained and qualified working in the insurance industry to participate as part of that process. Over the course of about a week and a half, these teams went out to all of Canfor’s facilities and undertook that risk assessment.”
The same process was underway at the 55 mills owned by MAG’s 12 corporate members. They opened their sawmills to each other so that collectively, safety managers could see what works and what doesn’t when it comes to sawdust control. That level of co-operation was unprecedented in an industry where the difference between profit and loss is measured in how milling technologies are applied. Mills do not share their secrets easily.
The CEOs’ involvement changed that and safety people began touring each other’s mills.
The union and the companies also worked closely together. The CEOs knew that no two mills are alike, and if the sawdust issue were to be corrected, MAG needed to catalogue best practices and share them with everybody.
Matters also contacted all the sawmill locals to assure them that dust management was a top priority.
“If anyone had any discomfort at all about sawdust, they were to stop work and start cleaning up,” he said.
Kayne took that same message to employees at the company’s B.C. mills.
At that point, May 2012, dust was still a theory; Matters was not yet convinced himself. But the companies and the union did not want to take any chances on a third explosion. Issues around past practices surfaced almost immediately: It turned out practices like getting out an air hose and blowing out the dust, simply put more fine particles into the air.
“Information was beginning to trickle out and we realized cleaning up these mills is a bit of a specialty,” Matters said. “This was evolving, almost day-to-day after Lakeland.”
The CEO Task Force also needed accurate science on what conditions create explosive dust before they could develop mitigation strategies and audit procedures. Cleaning up was a start, but until the issue was understood, there could be no guarantee there would not be a repeat.
“I’ve got to give credit where credit is due,” Matters said. “The CEO Task Force took this initiative based on their workforce, families and communities. This tells folks that for a brief time in its history, the industry really took workers as its No.1 priority.
“This had never happened before; getting everybody on board and working on the same page.”
In Nov. 2012, MAG’s efforts were recognized by the B.C. Safety Authority. It received the province’s highest safety honour, the Lieutenant Governor’s Award for its work on managing combustible dust.
In announcing the award, the authority, stated: “MAG has worked collaboratively with regulators, including BCSA, to facilitate compliance with the combustible dust hazard safety order and to develop an audit standard.
“MAG members have demonstrated compliance in their own facilities, and have worked actively to engage non-members in risk reduction efforts.”
The collaborative work among mills has been one of the keys in making the industry safer, Kayne said. Further, the attitude to sawdust on the mill floor has changed as well.
“Before, when I would walk through a mill, (managers) used to talk about quality, they would show me this new bearing, that new equipment,” said Kayne. “But now they know when I walk through a mill that I look up. I look at the rafters, I look at the beams.
“The awareness has changed.”
© Copyright 2014
Industry Intelligence Editor's Note: This article appeared in the Prince George Citizen as sponsored content on March 6 and is reproduced here with the permission of the Prince George Citizen and Canfor.
* All content is copyrighted by Industry Intelligence, or the original respective author or source. You may not recirculate, redistrubte or publish the analysis and presentation included in the service without Industry Intelligence's prior written consent. Please review our terms of use.