Millar Western returns Fox Creek sawmill destroyed by fire in 2008 to full production after investing C$60M in doubling capacity to 120 mmbf; official says confidence that market would come back helped decision to rebuild during 2010 downturn
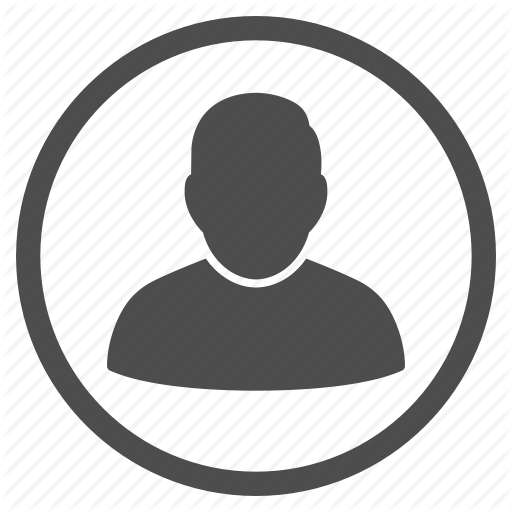
Wendy Lisney
CALGARY, Alberta
,
May 18, 2013
(Calgary Herald)
–
It was late in the shift when the blaze erupted, touched off by an electrical arc in the main breaker panel.
It took only four hours for Millar Western's newly acquired sawmill to be destroyed on that August evening in 2008. By the time the fire insurance payment came through in early 2009, the once profitable lumber market was in ruins.
Nobody was building mills then, because everywhere, mills were laying off workers and cutting back as much as possible.
But Millar Western is a lumber company to the core. So the firm started to rebuild in 2010 - a year when not one new mill was constructed anywhere in Canada.
"To rebuild at a time of a downturn! Well, some people looked at us and wondered what we were thinking," president and chief executive Craig Armstrong said at the mill's official opening last week - about 18 months after it went into production.
Stefan Demharter, vice-president of wood products for the firm, said the reason for the rebuild was simple.
"Millar Western has been in the lumber business for almost a hundred years, it was always lumber. We couldn't lose our feedstock for this mill, and we knew the market would come back."
Today, the Fox Creek mill is running at maximum output with one shift and sending its lumber - from the standard two-by-four and two-by-six boards to specialty sizes for decking and fencing - to customers across Western Canada. Its companion mill in Whitecourt, which has a rail link, turns out lumber for export to the U.S. and Asia.
A private company based in Edmonton, Millar Western sunk $60 million into its new mill. The state-of-the-art plant can produce 120 million board feet of lumber per year, twice the capacity of the former mill using the same number of staff, 68.
At the time of the rebuild, as luck would have it, a mothballed sawmill in Prince Albert, Sask. had equipment to sell. Millar Western bought an entire building and steel floor, with log decks, conveyors, de-barkers, dry kilns - and integrated all of it into the new Fox Creek mill.
The milling process starts with the arrival of logs from as far as 200 kilometres away - 55 truckloads of up to 800 logs apiece. The logs have already been cut into 16-foot segments - a much more efficient system than the traditional method of hauling full-length logs out of the bush. Each day, about 22,000 logs are unloaded either in the log yard or directly onto the log deck that feeds the mill. The diameter of each log is relatively small - minimum size at the top is just four inches, maximum size at the base is 22. Anything larger is set aside for a mill that uses the traditional head-saw system.
"These are not young trees; some of the ones with four-inch tops could be 200 years old. That's what you get in the boreal forest," said mill operations manager Tom Thompson.
The trick is to get the most from these small trees. The logs are scanned by computer at 1,000 points as they enter the mill, and the computer decides how each will be cut by the automated system. A slightly curved log might yield three lengths of two-by-four between 10-and 16-feet. Traditional saws would be able to cut only the longest board, while the rest would be turned into wood chips or burned.
The whole process is incredibly fast, with five boards of varying dimensions produced every two seconds. And the process is all recorded, much like a PVR, so staff can study reasons for any problems in the plant on a frame-by-frame basis.
The rough lumber is automatically sorted and stacked, dried for 24 hours in a kiln to achieve the desirable 16-per-cent moisture content, and sent to the planer for final trimming and grading.
An automatic grading system, the type now becoming common in Alberta mills, X-rays each board to determine its faults, and grades it for quality - top-grade lumber commands the best price, and foreign markets like Japan insist on it, as well as a higher "appearance" grade.
"We used to do this by hand, flipping boards as they went by and grading with a crayon. This led to a lot of physical problems with wrists and shoulders," said Demharter, an old grader himself.
Millar Western is determined to avoid another fire, and has the entire complex set with alarms and sprinklers, with a large pond outside for firefighting. Inside, the computer and electrical systems are all in secure, cooled rooms. "We keep this place spotless. This is not at all like a traditional sawmill," said Thompson. dcooper@edmontonjournal.com
* All content is copyrighted by Industry Intelligence, or the original respective author or source. You may not recirculate, redistrubte or publish the analysis and presentation included in the service without Industry Intelligence's prior written consent. Please review our terms of use.